Ear on Chicago; Electric Power
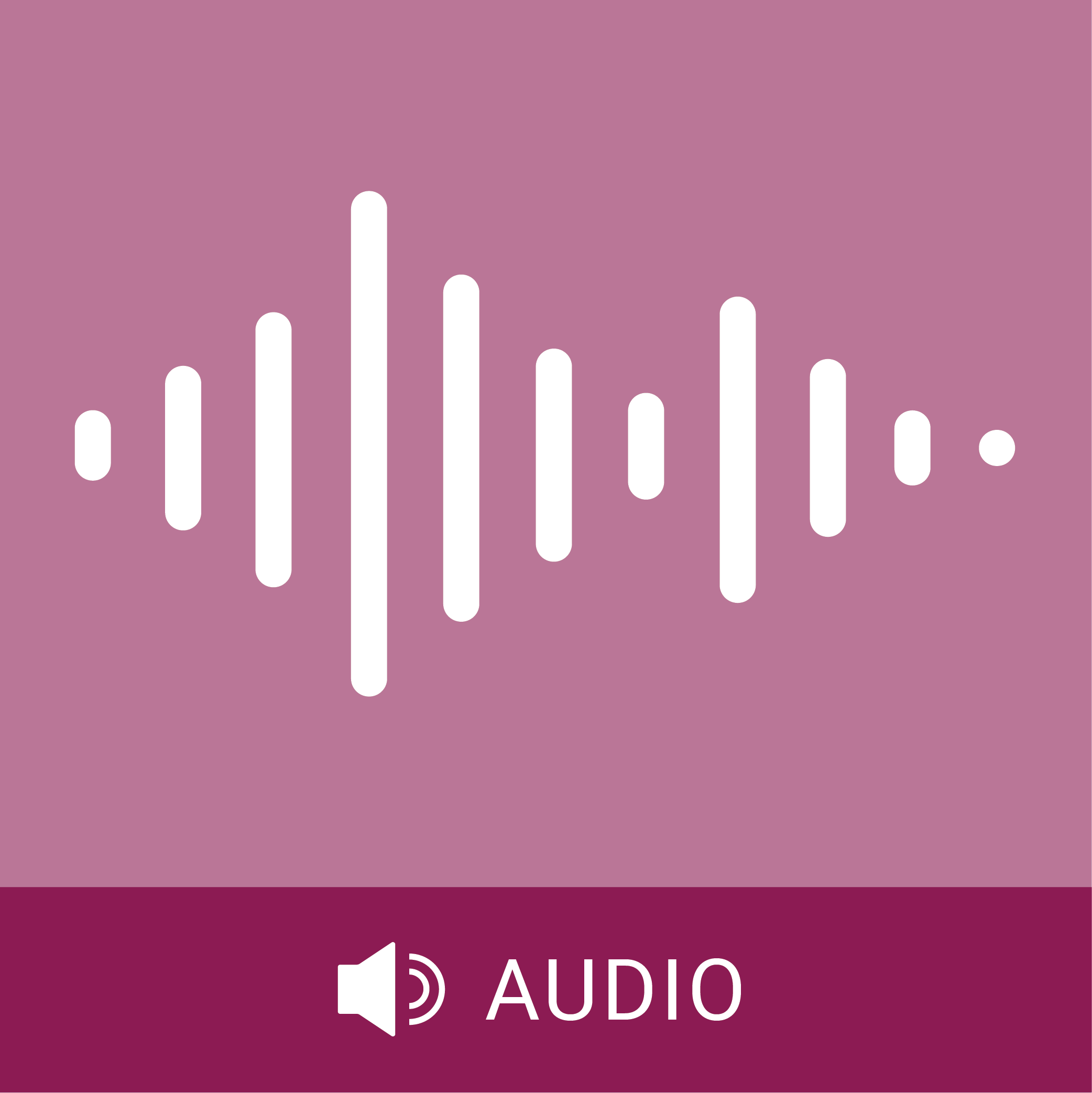
- Transcript
We're about to tell you the story of power, the production of power, its transmission to you in your homes and on your jobs. Our microphones are located at the Richland station of Commonwealth Edison. It's part of the Commonwealth Edison system that serves a population of more than six million persons. In an area about 11 ,000 square miles in size in Northern Illinois, including Chicago. In the system, of course, our Commonwealth Edison company and its public service company division. There are 12 generating stations in the system, part of one of the largest power systems in the country. Generating capacity now exceeds 3 ,750 ,000 kilowatts and scheduled additions will raise that figure still higher before the end of this year. The generating stations are all interconnected by transmission lines of various voltages. Richland and the other stations in the immediate Chicago vicinity are connected by high -tension transmission braids. The whole system operates as an integrated unit and generation is assigned to each station so as to obtain the maximum economy consistent with safe reliable
service. So let's begin this story of power, beginning with its production, then its transmission, and finally to you in your homes and on your jobs. To begin this story of power, the production of power, we're standing now in what I'll call as a layman, the yard of this Hanson -Niet modern appearing Richland power station, located southwest of the city of Chicago, standing with the vice president for Commonwealth Edison in charge of engineering construction and operation, Mr. Murray Justlin. Mr. Justlin, from here I see many things, buildings, huge towers, and tremendous stacks of coal. I suppose we can start our story of power with the raw materials and what I'd be correct if I said they were water, coal, and air. Right. Well, taking a look at these coal piles, they look like enough coal to run the whole city of Chicago, how much coal do we have and do we use around here? We have 725
,000 tons of coal stored here, we burn 6 ,000 tons a day in this station alone, and our system consumed over 38 ,000 tons on some of the hot days this summer, or 10 million tons last year. I think this demands a bit of an explanation, why would you be consuming so much coal on the hot days we had this summer? Because of the large heavy air conditioning load that our customers demanded of us. Here is Verne Stone, manager of production. All right, let's begin our story of the use of coal, it arrives by a barge, and what do you do with it? All right, the coal comes in by barge, each one of these barges holds in the neighborhood of 12 to 1300 tons. It arrives along our dock here, it's either unloaded into our storage piles or it's unloaded directly onto the belt, and shipped into the house by a belt conveyor. As you see standing here in front of you here is what we call our breaker house. Yes, what does this do? Well, the coal is rather coarse
when it comes up in these barges, or chunks in there that are 4 inches on a side or 6 inches on a side, it has to be crushed down for consumption in the cyclone furnace. How small do you break it down? It travels in on the belt, goes up to the top of this building, goes through what we call the large breakers, where it's reduced appreciably in size, it drops down to this equipment here at the base of the building, where it's reduced down to a quarter inch minus in size. From there, it is transferred on this belt conveyor that you see here to what we call the junction house, from there it passes on that incline conveyor up to the top of the building where it's transferred to the bunkers. And this crusher is working 24 hours a day, I suppose. We do not have to operate on that basis, we normally are able to supply this building in an 8 -hour shift. Each conveyor is capable of handling 800 tons an hour. All right, let's pick up our story from inside the building when the coal has finished its trip on the conveyor, it will
arrive where it will arrive in the bunkers above the borders. So our next stop will be at the boilers, the next stop will be at the boiler room yesterday. Now for step two in the story of power, I'm standing in what I'll describe as a great faulted room, a maze of pipes, wires, that macularly clean, great pieces of equipment, and in this room you get the feeling of power because there's a type of vibration and intensity about the whole building that perhaps our microphones pick up, which just mean the word power to me. Mr. Stone, we're standing now directly in front of these cyclone furnaces, are we not? Yes, a bay are standing directly in front of a boiler here that's supplied by four cyclone furnaces. And this is the main operating aisle or main operating floor in the boiler room. Wouldn't you like to step up on this next platform here and take a look into one of these
cyclone furnaces? All right, so suppose we do that, I'll follow you. We're now climbing a narrow metal stair onto a metal grill walkway, and now we are directly at the mouth of one of these tremendous furnaces, is it all right to look into this inspection hole? It is all right made to look in there, but don't look too long without colored glass. All right, I'll take a quick look. This is probably the brightest flame I've ever inspected, and tell me about what's the capacity, the temperature of these furnaces? About 3 ,000 degrees Fahrenheit inside this barrel that you're looking into. I think perhaps we can describe it best if we step back away, and you and I will be able to hear each other think and talk if we move away just a few feet. Now back again, out in front of the furnaces and the boiler, suppose we pick up the story where we left off Mr. Stone out of the coal pile, and you tell us what's happening in this building. All right, I'll try and describe this boiler. You realize that we're standing here and just see one floor to be exact, and
this boiler is approximately 10 stories high, equivalent to a 10 story building. We left our previous talk out in the coal handling system, and I mentioned there that we had the coal up as far as the bunkers. Well now let's follow that cycle further through the plant. How high do you raise the coal before you drop it into the furnace? In the neighborhood of 120 feet, that coal flows from the bunker down to cold scales through cold gates, and into the cyclone furnace, as you see here before you, just prior to its entry into the furnace, air is added to the coal, what we call primary air. As soon as it enters the cyclone, it is met there with tertiary air or helping air to push it through the throat of the cyclone. As it enters the main barrel of the cyclone, secondary air is added to the coal. That gives it the whirling action or the cyclonic action from which the
unit has derived its name, complete combustion of the coal takes place in this horizontal cyclone barrel. I think perhaps we can explain that name cyclone a little bit, in other words as I face the mouth of this furnace, there's a movement in clockwise fashion, is there not? That is correct. They could be either clockwise or counterclockwise, but it's a whirling action. It's like a barrel laying on its side and a whirlwind going on inside the barrel. Well now Mr. Stone, we've added the air to the coal in the cyclone furnace, as opposed we pick up our story there. All right, as I told you that complete combustion takes place inside of this horizontal cyclone, and in that process the slag or the ash, I should say, is removed from the coal and it's removed 85 % of it as a slag. The molten slag follows along the lower surfaces of the cyclone
and passes out through an opening, flows down as a liquid into the bottom of the primary furnace. From there it passes on to an opening in the bottom of the furnace floor where it pours as a liquid into water and disintegrates into a very fine black product. The heat from the combustion of coal passes out through the throat of the cyclone, passes downward through a screen wall. Then goes up through the secondary furnace, passing over the secondary superheater, primary superheater, economizer, down through the air preheater, then over through an electrostatic precipitator from where the remaining ash, as we call fly ash, is removed by high voltage. Now when you talk about this heat moving, I think we better explain that it's moving over an area which is almost the distance
of a planet -aged story apartment building. Yes or more. It's a very large area and all of that area is absorbing heat from this coal as the hot gases move through the water setting. The hot gases start out as I mentioned before in this furnace at about 3 ,000 degrees Fahrenheit. They emerge from the stack in the neighborhood of 300 degrees. It seems to me that you're making pretty good use of the heat you generate here. We're trying to get every BTU out of this coal that we possibly can. But Mr. Stone, tell me what the job of this precipitator is. Well, Mr. Flynn, when you were outside and interviewing Mr. Josson, I heard you comment to him how clean the stacks look. Mr. Josson said, let's go inside and we'll explain how we do that job. Now I've just told you that the precipitator, that all the hot gases pass through the precipitator. They are laden with some fly ash. These
particles of fly ash take on electrical charge and are removed from the stack gases as they pass through the precipitator. From there, they go on to an Industraff fan or the gases go on to an Industraff fan where they're pumped up the stack. And this equipment that you're looking at here today is the most modern in the world. It's the best development in the art of removing solid particles from stack gases. If from time to time you hear a loudspeaker voice of the background, those are conversations between various employees here at Winsland Station, communicating with each other in the most efficient way possible over these vast spaces in this powerhouse. I'm Mr. Stone. We've talked about the course of the heat, the use of the cold, but we haven't mentioned water. Tell us about what happens to the water in this system. Well, water is one of the most
important items that we have to deal with, especially in the high temperatures and pressures that we're using today in the generation of power. The water that we use in these bottles here is lake water, comes from Lake Michigan. Yet, to drink, we consider very pure. As far as usage in these boilers, it has to be processed. It has to be completely de -meneralized. To get away from severe scaling that would occur inside the bottle tubes and resulting in their burnout. Now, this particular bottle you're looking at here consumes 730 ,000 pounds of water per hour. In other words, that means that for every hour this water operating at full capacity will evaporate 730 ,000 pounds of water at 1800 pounds of pressure and 1050 degrees. That is evaporated into steam. Now, the water, more or less, is a continuous cycle. It comes from the turbine
after it's done its work, comes from the turbine as a condensate. It's pumped back through boiler feed pumps to the economizer on this water. It goes from the economizer up to the main drum. From there, it passes down through the whole water setting to the water tubes, picking up heat. From there, it goes back to the drum and then starts out as a steam through the primary superheater back to a header and over to the secondary superheater. Between the primary superheater and the secondary superheater, water is added. The amount of water being whatever is required so that when the steam reaches the turbine throttle, it is at 1050 degrees. After that water has been added, the steam then passes through the secondary superheater and into the main steam header supplying the turbine. So in
other words, you're reusing a great deal of this water over and over again. It's a continuous cycle. Our makeup is just around a percent or so. Our amount of makeup water required in the operation of these waters. Now we've covered the entrance of coal into the furnace. We've covered the burning of the coal. We've covered the transfer of water into steam and back into water again. What's our next step, Mr. Stahl? Well, I would suggest we walk over and look at the device that consumes all this steam. Or let's go over into the turbine room and look at the turbine. We're now ready to begin what we might call step three in our story of power. Mr. Stahl, what's this tremendous device I'm looking at now? Right here before you is the high pressure element of 150 ,000 cross compound turbine.
This is the high pressure turbine section right in front of us here and you'll notice up on top there are a number of springs. Those are the springs that control the valve mechanism to admit steam to that turbine. Down underneath there's a similar set. In other words, steam is fed into the top and bottom of it. Steam passes through this turbine and drives this element here to our left which is a 50 ,000 kilowatt generator running a 3600 revolution a minute. This steam after passing through this high pressure element passes over to this other element here which we call the intermediate pressure element. From there it goes into this big crossover here which is the crossover connection to the low pressure element and you'll notice that the low pressure element seems to be the same size on both ends. Well, it's a what we call a double flow machine. Steam passes from the center
of this both ways in the low pressure element and after it has completed that they're gone that far it has done all of the work that we expect to get out of it. From there it passes on down into the condenser which is operating under about 28 inches of vacuum and where the steam is reduced back to water, condensed back to water and there it's picked up with the pumps and is pumped back to the water as I explained before. It's pumped back to repeated cycle. Now the low pressure element here is not as high a speed unit as the high pressure. This unit is an 1800 RPM machine, 1800 revolutions a minute and develops 100 ,000 kilowatts of power. These two machines are tied together electrically on the floor below which we do not see. From there the power that's been generated passes out through transformers and is stepped up to on this particular unit
here to 69 ,000 volts to go into the bulk power system of the Chicago stations. Now the words you and I are standing between two generators which in total produce about 150 ,000 kilowatts. That is correct, Faye and we have four such units in the station. In other words we have four 150 ,000 cross compound turbines in this station. The thing that impresses me as a complete layman in so far's production of power is concerned is the fact that everything seems to be going so smoothly with these tremendous machines turning at these high RPMs, 1800 and what was the other one? 3600 revolutions. I would expect to notice a great deal more vibration. I'd expect to hear more sound. How do you explain the fact that these things seem to operate so smoothly? Well Faye the keynote to good and continued operation of any unit is perfect balance on it. These machines are beautifully balanced.
They're only just a very few mills of vibration in any one of the bearings on the machine and you'll notice down here on the floor that while the floor appears to be continuous. So out this turbine room each turbine is setting on its separate foundation and that little strip that you see is just more or less an insulating strip so that vibration from one machine is not conducted to the other. I think I might try to explain in terms of size just what these things look like to me. The high pressure generator which is now over to my right is about again as tall as I am and I would guess what would I say 60 feet long. Something like that and maybe I can help you out on this one over here the low pressure unit. That is around 80 feet long about 24 feet high and probably 23 or 4 feet wide. One of the other things that impresses me not only here but also in the boiler room is the immaculate appearance of all of the equipment,
thinking of all the oil, the lubricants and so on. The fuel has to be used. How are you able to keep this place as spotlessly clean as it is? We think the keynote to good operating is good housekeeping and we try it all times to keep this plant clean as well as all of our other plants. Occasionally we do have cold spillage or something and it does dust you the place up a little bit but in the main the boys do a splendid job and it's just a ritual with them around the station to keep their equipment looking nice. Could you give me any idea of what cost is involved in these two tremendous pieces of equipment we're standing near now? Well I would give you a rough guess that an installation of a machine like you see today I am talking about the purchase of the turbine alone would be in the Obviously our microphones are now set up in a more quiet
location. We're in one of the most modern control rooms I've ever seen an immense thing filled with dials and various switches which is the nerve center the nerve heart of this Ritzland power station. Mr. Stone what happens here? Fe in this room the entire plant is controlled everything but the coal handling equipment. In other words the generators the turbines the boilers and even the switching to the lines is all controlled from this control room it is our first step in going to centralize control at when this station was built. Now I heard you comment on a lot of dials and gauges and so forth and I'm quite sure that you will come up with some questions that I can't answer so I'm going to turn you over to Bill Joyce here who is a senior control operator in this control room I'm sure Bill can answer questions you might ask. Bill let's start out by picking a sample
control section I notice one marked cyclone 14 what does that mean? Well let's the cyclone on boiler one number four cyclone and in front of you you see the controls that we have to control the air and the fuel going to that cyclone in other words we have to have the proper amount of fuel and the proper amount of air to give us our proper combustion. I notice these scales are all labeled there's air flow cold scale bypass cold feeder interlock total air damper cold scale cold feeder each of these things controls one of the ingredients going into the furnace so that's right actually the cold feeder is our main supply of our fuel and when we have dump gas as they call it our extra gas gas company has we can burn fuel gas in our boilers here. I see now directly across from me and on the wall so to speak are some more large dials for example
up at the very top there is this thing that looks like well how shall I best describe it like about 20 speedometers lined up that's that's about right actually the first group of instruments they're all in group of fours one represents each cyclone the first group there you have your total total air going to the cyclone the next group shows the operator is proper primary air the third group would be his gas pressure when we are burning fuel gas and the third group or the fourth group rather is the gas differential gauges now I also notice something that looks very much like a television screen what does that do well that that is a television screen we have that's a 10 inch receiver there and we have a camera up at the boiler drum which is approximately 100 feet or so above where we're standing and we have a wired television in other
words we take the picture on the drum level and we record it here so the operator can look at the picture that he sees here and makes certain that his boiler does have water in it in other words we saw men working around the boilers and on the catwalks out in the shall we say the boiler room proper but actually you people in this relatively quiet comfortable and spotlessly clean room with its maze of dials are controlling the operation of the whole affair yes here we control the operation of the boilers and of the turbines which in return is a result of that we control the electrical output of the station thanks mr. joys very much mr. stone now we produce the power we've got it moving through this control station and what's about to happen to it well now we have to get rid of it do we not all right we do that by means of transformers we generate power in this station at two voltages 13 ,200 and 14 ,400 volts that is that is the voltage on the windings in our generators from there the power passes
to transformers located outside from where it is stepped up to the higher voltage in one case it stepped up to 69 ,000 volts and then the other to 138 ,000 volts why do you step it up it comes back to the economics in the main bay in other words if you had to transfer pump water a great distance for example and the man at the other end the line just wanted so much water in a given length of time you would have the alternative of putting in a large pipe line and pumping it in at low pressure which would be at a tremendous cost or you could put in a small line and pump it to him at high pressure which would be a much lesser cost that is the reason we step up to high voltages in transmission is to reduce costs in transmitting of power so in other words you send the power out of here at tremendous pressure shall we say as a layman by the time it comes into my
house it's down to what it should be down if you have an electric range it should be down about 220 volts and of course you need a little 110 around to well now do you send out different types of power or power of different pressures for industrial uses and business uses as opposed to residential uses yes we do in some cases we transmit power to the customer at rather high voltages and he steps it down through his transformers or maybe transformers that we might have to the voltages required for his own consumption as a matter of fact we control time how does that happen well we control it in this manner most clocks in use today are the electric clock and they operate on the 60 cycle system there nothing more where they may have huge dials in the main they're just a little synchronous motor inside the clock mechanism which tie it is tied in with our electrical system now we can vary the speed
of the clock by running our machine slightly faster than 60 cycles or we can slow the clock down slightly if we run them a little below 60 cycles and that's one of our jobs is to keep the clocks on correct time we began the story of power some 29 minutes ago talking with mr. Murray Jocelyn here again is mr. Jocelyn to wind up our story for us mr. Jocelyn the supplying of power to these many customers of yours must really be quite a task yes for he it is quite a task there seems to be no end to our customers demands for electricity and it is our job to meet these demands when they come this is the biggest year in our history of providing new generating capacity two large units have been added already and a third will go in commercial operation in November these three total 527 ,000 kilowatts this is a nice problem of timing
also it takes about three years to complete one of these large units alternating current electricity cannot be stored and as I said we must be ready at the flick of the customer switch our construction expenditures will amount to about 125 million dollars this year and we expect to have to spend a comparable amount each year in the next four years we are of course looking into the future fire into the future for new energy sources an example of this is the 180 ,000 kilowatt atomic energy power plant to be located on the Illinois waterway about 47 miles south west of Chicago this unit is scheduled to go in operation in 1960
- Series
- Ear on Chicago
- Episode
- Electric Power
- Producing Organization
- WBBM (Radio station : Chicago, Ill.)
- Illinois Institute of Technology
- Contributing Organization
- Illinois Institute of Technology (Chicago, Illinois)
- AAPB ID
- cpb-aacip-f7f79c7aa37
If you have more information about this item than what is given here, or if you have concerns about this record, we want to know! Contact us, indicating the AAPB ID (cpb-aacip-f7f79c7aa37).
- Description
- Series Description
- Ear on Chicago ran from 1955 to 1958 as a series of half-hour documentaries (130 episodes) produced by Illinois Institute of Technology in cooperation with WBBM radio, a CBS affiliate. Ear on Chicago was named best public affairs radio program in the metropolitan area by the Illinois Associated Press in 1957. The programs were produced, recorded, and edited by John B. Buckstaff, supervisor of radio and television at Illinois Tech; narrated by Fahey Flynn, a noted Chicago newscaster, and Hugh Hill, special events director of WBBM (later, a well-known Chicago television news anchor); coordinated by Herb Grayson, WBBM director of information services; and distributed to universities across the Midwest for rebroadcast.
- Broadcast Date
- 1955-10-15
- Asset type
- Episode
- Genres
- Documentary
- Topics
- Education
- Media type
- Sound
- Duration
- 00:28:33.024
- Credits
-
-
Producing Organization: WBBM (Radio station : Chicago, Ill.)
Producing Organization: Illinois Institute of Technology
- AAPB Contributor Holdings
-
Illinois Institute of Technology
Identifier: cpb-aacip-4043bc985a9 (Filename)
Format: 1/4 inch audio tape
If you have a copy of this asset and would like us to add it to our catalog, please contact us.
- Citations
- Chicago: “Ear on Chicago; Electric Power,” 1955-10-15, Illinois Institute of Technology, American Archive of Public Broadcasting (GBH and the Library of Congress), Boston, MA and Washington, DC, accessed July 4, 2025, http://americanarchive.org/catalog/cpb-aacip-f7f79c7aa37.
- MLA: “Ear on Chicago; Electric Power.” 1955-10-15. Illinois Institute of Technology, American Archive of Public Broadcasting (GBH and the Library of Congress), Boston, MA and Washington, DC. Web. July 4, 2025. <http://americanarchive.org/catalog/cpb-aacip-f7f79c7aa37>.
- APA: Ear on Chicago; Electric Power. Boston, MA: Illinois Institute of Technology, American Archive of Public Broadcasting (GBH and the Library of Congress), Boston, MA and Washington, DC. Retrieved from http://americanarchive.org/catalog/cpb-aacip-f7f79c7aa37