City in Sound; Sylvestri Art
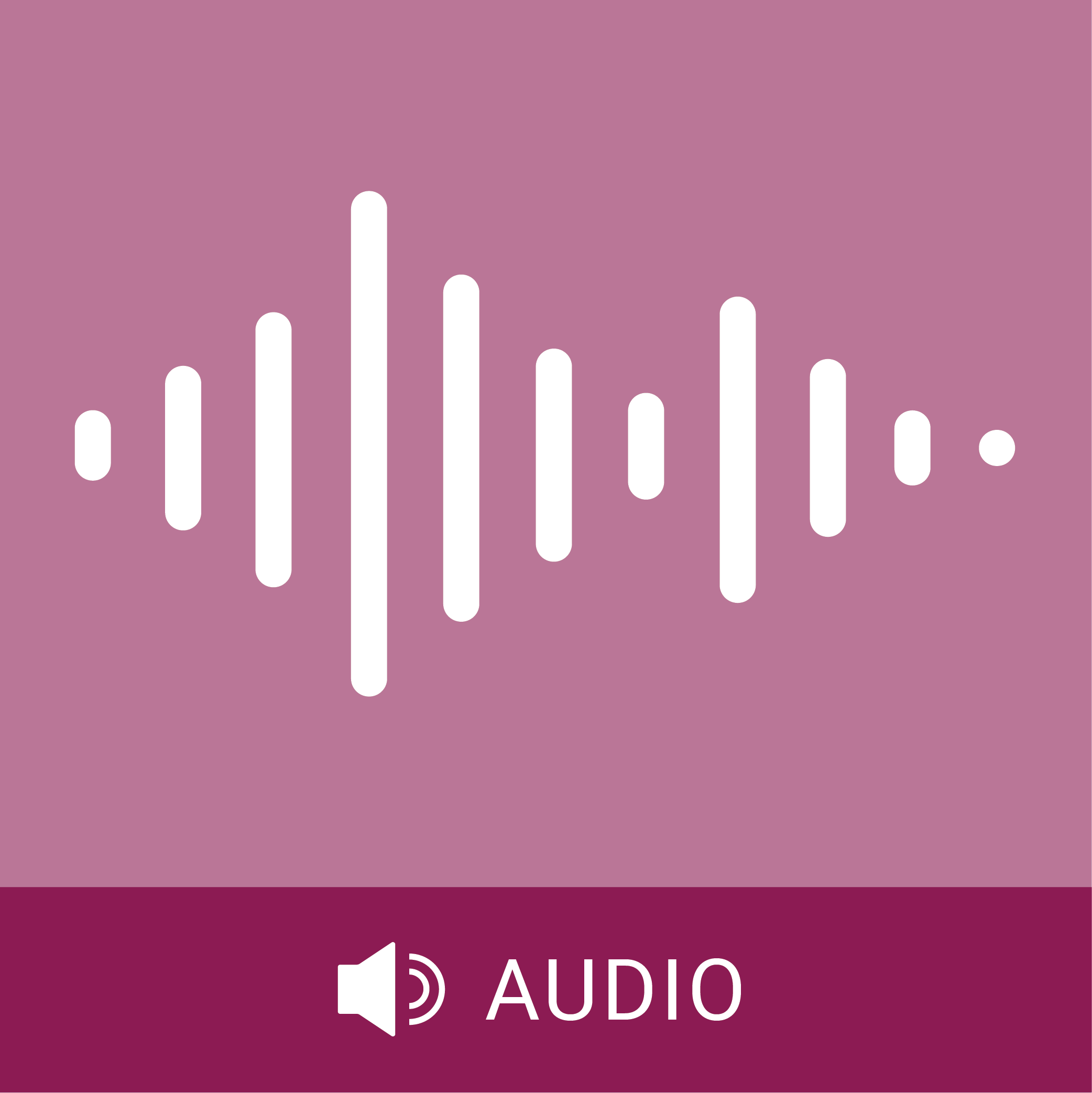
- Transcript
This is Jack Angel with City in Sound. These are stories out of Chicago. City of all things. Among them, an industry for art. The Sylvester Art Manufacturing Company is a complete industry. Close to the west end of the loop, it creates and manufactures art products and commercial displays on a great scale. It is an impressive amalgam of art and industry with a good part of modern science sculptured in. New materials, new techniques, play an increasing part in it. Make it a colorful call in our series for the Project Science Calling. Mr. Bernard Gorman, his vice president and partner here at Sylvester Art Manufacturing Company, should know a great deal about it and has been here how many years? 17 years. I left law school to come into this business. Oh, you wanted to be a lawyer. That's right. Now you're in the arts product. Arts products. How has it been? Well, it's been a fast
pace. It is very challenging. We are in the home furnishings field, the advertising, the gift field, and medical educational fields, and other facets of modern life and no two problems are alike from day to day. Mr. Gorman, there have to be a tremendous field because you have such a large plant here. You have well a factory -sized organization here. And I had no idea that an art product's manufacture would be a manufacturer on such a large scale. You told me some of the things that you manufacture. What are the big lines? Well, our big line is window display. We do windows for leading department stores throughout the country. Our big season is Christmas in which we do the large mechanical windows.
Isn't this kind of an expensive business to operate? It is very costly to operate. For example, we are now planning our next year's Christmas presentation. We have a budget, a lot of tar that of over a quarter of a million dollars. Wow. Now you say next year's Christmas. You don't mean 1958, but 1959. So here we are in September of 1958 and you're planning to head to Christmas of 1959. That is true. We have behind us spring, Easter, and fall of 1959. I see a number of foreign figurines around and some imports. Oh, Germany, Scotland, Bangkok. I am over there. Do you pick these up yourself? My partner and I travel the entire world and attempting to pick up the unusual on merchandising. The new trends in art, discovering the unknown artist. The
different and unusual materials that we might be able to use in our manufacturing cycles. Well, in that sense, your operation spans the whole world. It does span the world. Must be interesting. It's a challenge. Jim Small has a very interesting job here. He's the chief designer. Of course, it follows to ask him what a chief designer does in an art manufacturing company. Well, a little bit of everything, a little selling, a little publicity, supervising all aspects of the work. Surely you have a staff, of course, and I imagine a rather large one. But what goes into designing figurines and art products and the various items that you sell and retail? Well, basically, a need for a particular design. Either the customer has a purpose for this product or we try to anticipate their needs by designing a line or a promotion that we feel that they could use. Yeah, I was just looking down at some layouts here on a
1958 Christmas display window at B. Altman in New York. What in the world goes into all this? Do you design absolutely all of this? Well, to a large extent, for this particular order or for this particular company, we've done it several years in the past. They give us an idea of a promotion that they want to have made out and we attempt to fill their needs from a design standpoint. Well, let's see what the small fry of New York City are going to see at B. Altman's window here. The central figure looks like old mother Hubbard except the dog. Well, actually, it's a nursemaid or a nanny. The windows are of a period, about 1900. And instead of a typical nursemaid, Altman's idea was to use a big old shaggy hound dog who would be the nurse nanny to these children. In this particular case, they're a family of five or six children. They're all red -headed boys and girls
from toddlers up to six or eight years of age. The nursemaid is a Christmas character. She is a central figure of the whole display. And I take it, there's a lot of movement here. Yes, practically, all the figures, including the nursemaid hound dog, are animated. And each window, there are six of a series, tell a particular story or a scene. And for example, there's a kitchen scene, a bedroom scene, a bathroom scene, and so forth. Surely. Well, what do you find yourselves designing most of here, Jim? Well, that would be very hard to say. That's two complex of a question we do from the very smallest delicate kind of thing to colossal figures used for exterior decorations. Some as high as 30 or 40 feet, made in sections and ships throughout the country. Well, in your display room, there I saw such things as busts of Lincoln and, yes, and plates of Adam and
Eve. That's our basic line done in composition. And it's a stable line that stores, and as well as homes and offices you use throughout the year or at least we sell them quite frequently. Jim, what are some of the materials you use in the designing and the production of some of these items? Well, we use a tremendous variety of materials. We have to be extremely inventive at times. Many times there aren't materials available that might fill a particular need. But specifically, we work with rubber, cast rubber, liquid latex actually, various compositions, various plaster compositions. And other materials, one called salastic, which is a plastic impregnated fabric and soluble in a solution. Drys and hardens to a great degree. Of
course, fabrics for costuming and fur claws to be used as covering for animals and we're going to use a particular type of fur cloth for the curving of this hound dog we've been discussing. And of course, pieces of leather and many other materials, glass, plastics and so forth. Well, there are basic materials that you use. You find that new sciatific developments provide you with new types of materials. Yes, from time to time there are new things we've recently begun to work in vinyl plastic, which though not a new material is new to us and rather new to the display field. Well, as the plastic industry thrives and enlarges, it's going to provide still other materials for you. Yes, fortunately, the plastic industry is an extremely enterprising one, and they have in recent months or years attempted to show many small firms such as ourselves how to use their material. It's been, they have a wonderful educational program that we're taking advantage of at the present time. Well, I should say the designing phase is certainly a combination of the old stand -by
materials and that being provided by modern science. Yes, definitely. Modern science being very important and coming along great guns with us, or we're going along with it, I should say. Mary and Jaskolski, you're a sculptor in an art product company. Not just exactly what does that work, it's just a... Well, we make the models out of clay. The first thing we do with the armature and then after we're true with armature, we put clay over it and then we make the figure work or animals or anything when it comes along. In other words, for each item that comes out of here, there first has to be a sculptured piece, right? That's it. And then from the sculptured piece comes... They make the mold, because they're molding the department, they make the plaster mold for rubber or many other things, plaster or rubber. And then it comes up here to be sophisticated. And then this must be a very interesting job, and you certainly
must do a lot of sculpturing. Yes, we're doing. Were you a sculptor by profession, by that I mean, were you an artist? In the moment I came to this country, I land over here in Chicago. I'm still in Chicago. That's a 45 years ago. Were you a sculptor when you came? No, I came here to young 17 years old. A sculptor in Poland. Do you do any art sculpturing away from here? Well, I did at the very beginning, I did the building trade, as we call it. That means decoration on theaters and interior exterior. And then when this thing is over, it's finished. And while I started to work in a window display, it was a sculpture. Well, this must keep you off of busy making a separate piece of sculpture for every form and figure here in your workshop. Well, it takes up from three to two a week, one week, to make the figure. Well, when you consider that our professional and artistic sculptors spend many months on work. Well,
that's a different case. Yes, it takes, if it's a big figure and so forth, it takes a month and months sometimes to study. How about that big dog in the B. Altman Christmas display? Did you do that? I did, I did. How'd you do that? Well, the first thing I got the drawing, and then I started to build the armature. And when I'm through with armature, I just take the soft clay. What are the armature? Is that the skeleton inside? That's the form of the structure of the bone inside. I see. And then when you get this, then you start to put the clay over it, build it outside. Yeah, you can go to love a dog like that, can't you? Wait, it's worked with it for a long time. Why? Are you actually using a completed product? It's thick, so it doesn't take long, but it takes quite a lot of time. How big is that dog? It's about three feet. Three feet tall. Three feet in the head. Maybe they'll send you to New York and see how it comes out. That might be. Well, here on the fourth floor shop of Sylvester,
it's quite a scene to describe to you. It must look like what Santa's workshop would look like. There are just thousands of forms, figures, ranging from very small to very large. I see a minute and various machines, band saws, and tools working on figurines and forms, and some ladies, children. I'm going to ask Mr. Paul Zoolock here who's in charge of the paper mache operation to describe what his operation is in all this. Well, our operation is to cast, as we call it, certain items which have been sculpted and went through mold making process to cast him in a proper medium. Now, before, let's say, years ago, a medium was paper mache, and the name is still sticking to us. Actually, we are not doing any paper mache work, we're using more modern mediums, which range from natural latex, synthetic
latex, and various plastics and resins. So, first of all, the sculptor is made of whatever form you wish to duplicate. That's correct. And then, eventually, it finds its way up to you to cast. To cast. Where will he go now, Paul? The finished item here. Let's take this immediate vicinity here. These latex form objects, the angels and the children, and all those little dolls over there, those little forms that look like dolls. It depends on the end use of an item. Let's say this particular item is just a static figure, which requires finishing and dressing. Now, we have many mechanical items, which are going to be animated as an end product. In this instance, we have to break the bodies, position them, keeping in mind the true action of a figure, and
we're working very close with mechanical department. Now, those positions figure go to mechanical department, and those people are putting mechanism, in many instances, very intricate one. And we are getting them back for patch up, job, and smoothing out, and potting out. Now, I would like to mention, and whatever we have here is a Sylvesteris development and product, but this firm is very modern. And we have full opportunity to check new mediums and new materials, and we're taking advantage of it. Wonderful. So it's very important that you're able to break it. That's correct. I used to study chemistry, and that helps a little bit too. Well, that's very interesting that a designer, or at least certainly a fabricator of art products, should be a chemist. Well, it's not necessary. At least he should have a basic knowledge and keep with the trend. You know, it's material as well as design. That's correct for time of paper mache is actually over. We have more modern faster
mediums, and mediums which can take abuse in an end product, which works to advantage of fabricator and the consumer as well. Where will these items be going? Do you know that into a display? Oh, they go. Yes. Most of them they go for display purposes in windows or various department stores, all over the country as well as abroad. Well, the thing that interests me here, you apparently just have one mold, one sculptor, for one item to be fabricated. That's right. Well, that must be a very expensive thing. You don't run off a couple of hundred or a couple of hundred hundred in volume production. You go through this whole process just for one finished product. Well, it seldom happens that a customer orders just one figure or one unit. Well, one type. One type? Well, they do order one type, but those figures have been performing different
animations and appear in different windows differently on different background. So the job is more justified. Of course, we have a more or less production items, like over there on the far bench, you have medical models, of course, so they are done again in different mediums, different synthetic latex, and those pieces are done in natural latex. So we have production, too. Well, now they call Mr. Ross McKenzie a mechanical designer. He's the man that makes these displays gold, the next move, the arms way, the feet walk and whatnot. How do you do this? Well, sometimes the idea begins with us, and many, many times they start with the customer, and then we talk over the possibilities, and from then on we take it and try to create what they've asked for. Many times it's something new, many times it's something impossible, but at least we will try it. We try to apply scientific and physical principles using,
we've had great success in water effects, using air, lights, and smoke effects from dry ice, little stoves in the windows that are smoking at intervals, and creates some very realistic illusions. Basically, we've discovered the ways to make fire without using fire, with revolving drums and flashing lights, and we've also found an application of silk that makes it a very real looking fire, since you can't have a real fire in a display window. Each case has its own challenge, isn't it? That's right. Recently we've developed a means of synchronizing different units that are perhaps dancing or playing instruments in a window without having a mechanical hookup. We call it a cadence timer, and any unit that's built for it can be hooked up and placed anywhere, and it will keep time with music, with
the unit, with the other units that are going on, so they're all in perfect synchronization. We've also had some very nice success with the use of electronics to have figures singing, and their voices are controlled by the peaks or the accents in the music, so that they are in perfect timing with what they are saying or singing. You have to be an engineer as well as a designer. We're always experimenting with new angles and new lines. Are you mixing electricity? Always trying to create something new for the customer. Most of the motive power is electricity, isn't it? Yes, without electricity we'd be lost. However, this year I am throwing around with the idea and have accumulated some samples that may be possible to control an entire window by the use of compressed air. But that again is experimental, and we do a great deal of that sort of thing. How about this Altman dog now? The dog is going to be in the window and walk around and act quite human and move his arms and legs. Well, in this
particular series or theme, the dog doesn't walk, but she turns. The dog is the nursemaid for the children, and so we have pictured her as a costume of the dog as the nursemaid. So the big bass at town is the baby sitting, and she reads to the men out of a book, she rocks in a chair, she falls asleep, in another picture she's in the cellar with the children, and they're all making toys with Christmas. She is at the furnace, and she's talking to them, turns her head, and tells them what to do. All right, is this all done by a series of motors? In the motor? In timing mechanisms. More and more today, people are asking for their figures to do more than just repetitious animation. And in order to tell a story, we must have electric controls, which we call a timer or more flowery expression, a synchronizing mechanism. This we build, we
build ourselves, we do our own electric schematics, and plot all the cams that make these things tell the story. Well, I had no idea that the art products business was so scientific and brought into play some of the leading technical sciences of our times in our system. Boy, you can make Santa Claus do about anything, can't you? We sure can, at least we try. Well, these figures and characters and the art objects are beautifully finished, display models, and instrumental in finishing them is Louise Brown in the finishing department. Exactly how is this done? Well, after the figure comes to us, there is the animals especially. We have to cover with fur, so we have to put this fur on, in a way that you can't see where it's joined together. And of course, the birds. We'll actually use real fur, Ms. Brown. Well, it's a special fabric fur that we use. On some of the animals, we do use real fur. And
we use a brush to blend this fur and so you can't see where it's joined together. Of course, as far as the dress and his concern, most of the time, the designer has seen in what design they want for the dresses. And do you make the costumes? Yes, I make the costumes, and sometimes the design, I have to change, and according to the action of the figure. You have to be kind of a very special seamstress there, no? Well, somewhat. And it's much more difficult than sewing for people, because of the action of the figure, and there's several movements there that you have to allow room, and all is to keep them labor in the motor. And the joints that are open, we have to use rubber sheeting to keep the fabrics from being all year wearing, and that way we won't have any trouble. And some of them, we have to allow in this show list, for the action of the show list, and make sure something of the kind, sometimes. Do you use just ordinary cotton or wool
cloth, or just ordinary commercial fabric, or is there a special type? No, we use ordinary commercial fabrics of all types. And some of the customers says they own fabrics, which we don't have to wear about. But we have all their hair to do up there, and some of the hair we have to dye our sails, and we can't get the shade that the customer wants. What material do you use for hair? Well, we use saran. Hair. That's a special hair that is used for this particular kind of business. And we make the shoes, stockings, and everything. So once they're finished, they're just about, like there's nothing left at first. The Indians who fashioned clay bowls by hand and painted them brightly with the dyes of the desert would look on with utter disbelief. The Sylvester company could make it any size, any shape or color in any quantity, and tuck it away almost unnoticed among the hundreds of its other products.
This is creative art, big business, and another Chicago industry. This has been a document in the series Science Calling. And this is Jack Angel with George Wilson, an engineer whose recordings here have imprinted city in sound.
- Series
- City in Sound
- Episode
- Sylvestri Art
- Producing Organization
- WMAQ (Radio station : Chicago, Ill.)
- Illinois Institute of Technology
- Contributing Organization
- Illinois Institute of Technology (Chicago, Illinois)
- AAPB ID
- cpb-aacip-d64afd14b13
If you have more information about this item than what is given here, or if you have concerns about this record, we want to know! Contact us, indicating the AAPB ID (cpb-aacip-d64afd14b13).
- Description
- Series Description
- City in Sound was a continuation of Ear on Chicago, broadcast on WMAQ radio (at the time an NBC affiliate). City in Sound ran for 53 episodes between March 1958 and March 1959, and was similar to its predecessor program in focus and style. The series was produced by Illinois Institute of Technology radio-television staff, including Donald P. Anderson, and narrated by Chicago radio and television newscaster, Jack Angell.
- Asset type
- Episode
- Genres
- Documentary
- Topics
- Education
- Media type
- Sound
- Duration
- 00:23:27.024
- Credits
-
-
Producing Organization: WMAQ (Radio station : Chicago, Ill.)
Producing Organization: Illinois Institute of Technology
- AAPB Contributor Holdings
-
Illinois Institute of Technology
Identifier: cpb-aacip-2ac351fa25e (Filename)
Format: 1/4 inch audio tape
If you have a copy of this asset and would like us to add it to our catalog, please contact us.
- Citations
- Chicago: “City in Sound; Sylvestri Art,” Illinois Institute of Technology, American Archive of Public Broadcasting (GBH and the Library of Congress), Boston, MA and Washington, DC, accessed August 10, 2025, http://americanarchive.org/catalog/cpb-aacip-d64afd14b13.
- MLA: “City in Sound; Sylvestri Art.” Illinois Institute of Technology, American Archive of Public Broadcasting (GBH and the Library of Congress), Boston, MA and Washington, DC. Web. August 10, 2025. <http://americanarchive.org/catalog/cpb-aacip-d64afd14b13>.
- APA: City in Sound; Sylvestri Art. Boston, MA: Illinois Institute of Technology, American Archive of Public Broadcasting (GBH and the Library of Congress), Boston, MA and Washington, DC. Retrieved from http://americanarchive.org/catalog/cpb-aacip-d64afd14b13