Ear on Chicago; International Harvester Research; Part 1
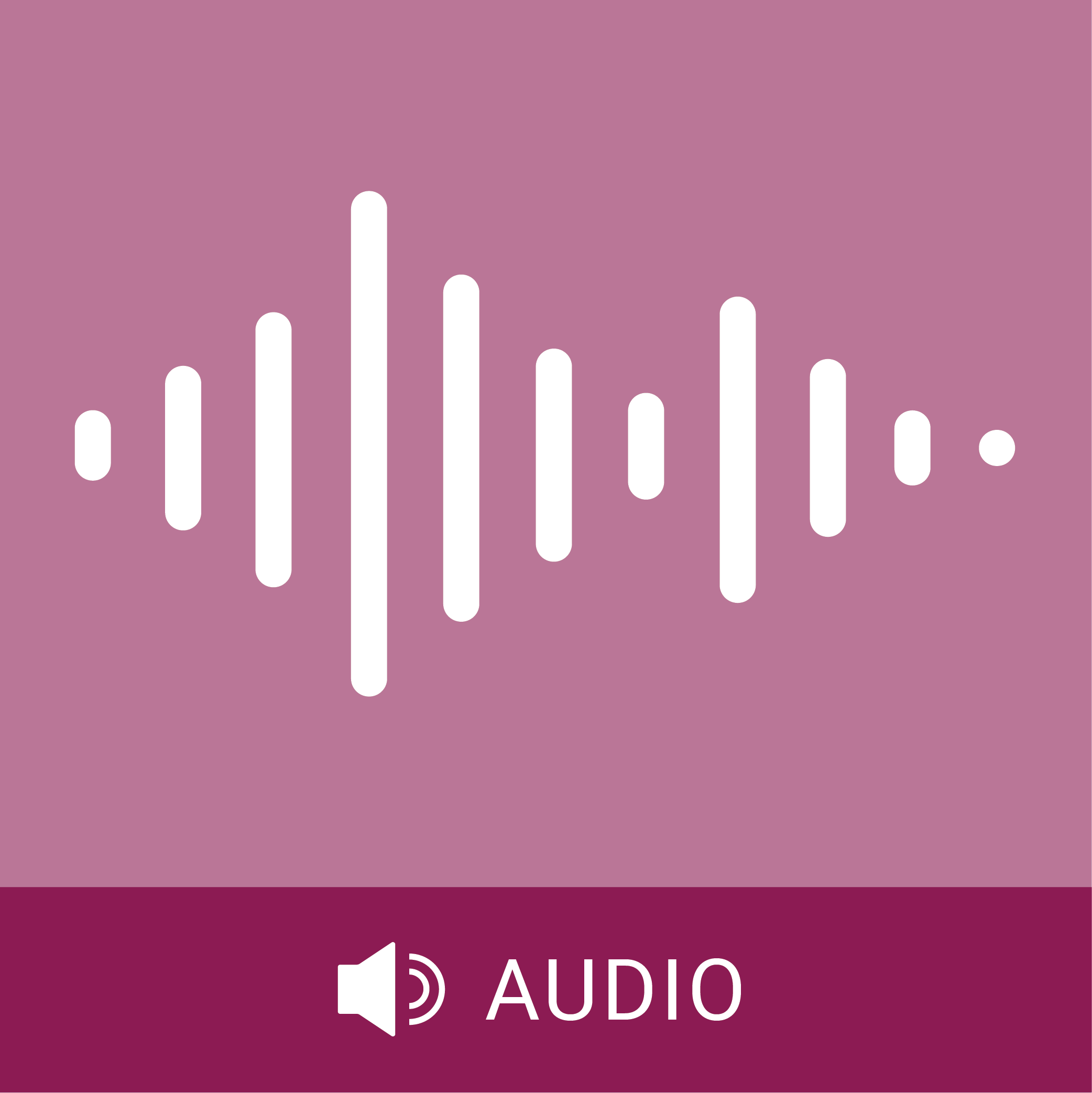
- Transcript
That was the sound of a jolting machine located in the experimental foundry of the International Orbiter Company's manufacturing research labs located on Western Avenue here in Chicago. In this center, the company's 21 production plants are provided with the facilities to keep abreast of the latest developments in manufacturing methods. We are now in the office of Mr. W. D. Bryson, the manager. Mr. Bryson, would you tell us something of the formation and the purpose of manufacturing research? After World War II, top management and art company saw the necessity of establishing a central facility in the field of manufacturing research. This facility was established during the year of 1946 with these primary objectives to study and conduct research in the field of manufacturing methods, techniques and processes and also in the development of new materials. One of the other main objectives at
research was to formulate standards and manufacturing practices. Also, we were established to give assistance upon requests to our manufacturing plants and our engineering departments. Mr. Bryson, tell us something of the scope of international harvester company's operations. Well, many people are of the opinion that the international harvester company manufactures only farm equipment and farm tractors. However, we do have a very wide diversification of product. We manufacture motor trucks, industrial power products, such as color type tractors, industrial power units, off the road equipment. We also have a steel operation and a binder and billar twine operation. What about the operations here at manufacturing research? We have approximately 200 ,000 square feet of floor space. We're situated on approximately 10 acres of land.
We have a capital investment of nearly $5 million. In the present time, we have 330 employees, 75 % of whom are technical. Well, now Mr. Bryson, I suppose we're ready for the tour of the plant. Yes, we are, Mr. Hill. And at this time, I'd like to introduce you to one of our engineers, Wayne Drum. Fine, thank you very much, Mr. Bryson. Where do we go first, Mr. Drum? Well, they are pouring some nodular iron in the foundry, so I suggest we go there first. Well, here we are in the foundry, Mr. Drum. And I suppose the first thing we should start with is the operation over here, which is the only one that I can see in the general area, which is working at the present time. Would you tell us something about that? Well, to do that, I'd like to introduce to you one of our foundry supervisors, Sam Johnson. All right, Sam, what do you call this piece of gear over here? Well, at the present time, we're getting ready to tap out an electric furnace, and we're preparing to make a heat of
nodular iron. nodular iron is a new material. It is similar in composition to gray irons, but it has a magnesium addition. As the metal comes out of the electric furnace, you will see a considerable flare, which is the reaction of this magnesium with the molten iron. Well, Sam, what was those whistles we just heard? That's the warning whistle that the heat will be out in a couple minutes. Warning, who? The all the crews so that all of our men will be prepared to be around and handle the iron when it comes out of the furnace. Was this a dangerous operation? No, sir. It's not pretty any more dangerous than handling molten metal is. A certain precautions have to be taken. It can be dangerous if it's not handled safely. I'm just wondering, Sam, we're standing rather close. Well, not too close. No, sir, we're not too close. We're 30 to 40 feet away from the molten metal as it comes out of the furnace here. And it'll be coming out any bit of that. Yes, sir. As soon as this ladle is in place, we'll be
tapping out the furnace. The ladle is being moved into place right now with a large crane. A truck has just moved it in on a dolly. The dolly is put in place, and now the crane is going to lift that large ladle over into position. Sam, what's that ladle made out of? Well, the ladle is a steel ladle, but it's lined with a refractory that insulates and holds the molten metal. If you notice, there was an addition that was just added to the ladle, and that's the magnesium alloy. Somebody just poured that in. Yes, sir. He just dumped it in. The ladle is now being lifted by the crane, and will be put over into that pit. You have a technical term for that pit over there. No, sir, it's just a pit. Just a plain ordinary pit. All right, the ladle is being moved over now with the magnesium inside of the ladle. It'll be dropped down just below that furnace, and I suppose that the molten fuel will be coming out any second out of that out of the
spout on the furnace. Yes. What kind of a reaction will we get here, Sam? Well, we'll get a rather violent reaction, or it looks very violent. We'll get a white flare coming up, which will be the magnesium vaporizing, a considerable percentage of it vaporizes as the molten metal hits the magnesium. Now, one of the workers over there is just taken out a large ladle full of molten metal, and he's pouring it into something. What is that, Sam? He's taking a test sample on the heat to see if the iron is ready to be tapped from the furnace. Just been notified that they have 15 seconds before they tap out, and now they're ladled. The spout is being moved down, and there is the magnesium igniting, and the very brilliant flame, which Sam said a moment ago, we wouldn't be able to look at, and how true that is. That's a magnificent sight to see, Sam. Is it, I suppose, more useful than beautiful, though, isn't it?
Yes, here we have a great many applications for nodular iron. Many of them are future developments that will be coming along with material, but it is a new product. Primarily, it will have application and replacement of steel castings, and in some cases forging. Just what exactly happens to that molten metal as it hits the magnesium? Well, the magnesium is in a form of an alloy. It has some iron with it, and when the molten iron hits it, the magnesium itself vaporizes, since it has a melting point that's considerably lower than the molten metal. That's the brilliant fire we saw? That's the brilliant fire, and of course you lose a good bit of the magnesium as it burns up that way, but we retain a very small percentage in the molten metal, which does the job that we're after in the nodular iron. You people keep talking about nodular iron. What exactly is nodular iron? Well, a
new type of material that has many of the characteristics of cast steel, and many of the characteristics of gray iron. Primarily, it's easy to melt, similar to gray iron, and then it has some of the ductal characteristics of steel. What would be one specific use that nodular iron would be used for? Well, one job that gives a good application of nodular iron is a cotton picker arm that was formerly made of a forging and then welded. Now it's made as one piece in a casting of nodular iron. Sam, a little while I understand you're going to pour a mold, is that right? Yes, sir. As soon as this metal is brought up out of the pit, we'll go around here and pour a green sand mold. We watched the large ladle of molten metal being poured into another container, and the containers being moved over here now where they're going to pour the mold. Why do you move it into this other container, Sam?
Well, the holding ladle that the material that the metal was tapped into from the furnace, it's too large to bring it up in this bay to pour the mold, so we've transferred into a smaller ladle for actually pouring the mold. Now it's actually being poured into another smaller ladle. What about that? That's for our test samples again on the iron itself. Now what do you test it to see how hot it is and if it's the right temperature and so on? No, specimen, well we do that too, but specimens are being poured there that will later be analyzed for chemical analysis and physical characteristics of the iron. Now this large ladle is being moved into position on top of a huge rectangular shaped black box, it looks like to me. Is that the coffin, Sam? Well, that's a sand mold. The black color is from the powdered coal, the sea coal is the term it's used. I mean, that's actually sand, he's pouring it. Yes, that's a sand mold, the cavity inside of it,
which will be filled with this molten metal. All right, now I see that the metal is being poured out of the ladle and once again it gives you a brilliant light, but certainly not as much as when the magnesium ignited. But it's going into the mold now and what will happen to it once it's in there, Sam? Well, once the mold is filled, we'll stop pouring and the metal will cool and set up in a solid state. Now what do you do with that? Well, then that casting will come down and be shaken out and operation we'll see a little later and go to the cleaning room for cleaning and we'll have a final casting which will be the basic part of some product. Now you mentioned the joling machine, that's what we're standing in front of right now, is this Sam? Yeah, yes sir, the sand was just vibrated onto the machine and the motor is riddling the sand into the flask. Now you see putting some more sand in there, it's a vibrator, pushing the sand over into the flask. Now what will come out of all of
this? When he gets through making this mold, he'll have one of the sand molds that we pour iron into. He actually makes the mold by hand. He's just placing the placing the sand in there at the moment, there'll be a mechanical action as you see now on the joling to form the mold. That's the joling machine. Yes sir, that's the joling machine for making a sand mold. Sure hear that. We've come now to the shell molding and core making operation which is only a few steps away from where we were talking about the joling machines. Now would you tell us about this particular operation, Sam? Well this machine that we're standing by here is a new machine for producing shell type cores or holotype cores and they differ from a conventional core.
In that conventional cores are made of sand and bond with oil which requires baking for a period of three to four hours. Now with this new type process, the sand is bonded with a phenolic resin and we can do the whole operation of flowing which is the method of introducing the sand to the core box. We can blow it and cure it in the matter of order of a minute's time and the core is ready for use in the foundry then. Now Sam once again we're talking terms and we get back to the term of shells and cores. Would you tell us exactly what that is? We looked at one little while ago. Well first a core is a what is used in casting to form a hole in the casting or form an internal shape. Now this particular core that we're going to witness being made here is a port core which forms a cavity in the
head of an engine. It forms the cavity through which exhaust gases leave an engine. We also have the type that would convey the intake gases to the engine. It's air pressure Sam? Yes this machine is run by air and then has gas oven on it for or gas flame on it for sureing out the resin in the core. Don't tell me the operation is complete already. The core has been formed the machine rolled over there and blew a sand resin mixture into the core box and it's now being cured. In a matter of well now the box is opening up and we have a finished core that could be
taken and put into a mold. We've heard about core making. What about shell molding Sam? Well this machine that we have before us here is a machine that makes shell molds by the dump process wherein the sand resin mixture is dumped on top of a hot pattern and you get a shell type mold instead of having a heavy sand mold as you have seen previously out here in the foundry. Well now this makes only half of the shell is net correct and you make put the other half together make it one. Yes we make two pieces as in our other molds only in this case we have two shells that are mounted together. The machine now going to run through its cycles and there again is an air actuated machine. It turns the pattern upside down then the upper box comes up and engages and drops the sand resin mix on top of the pattern. There's a short investment time
then the machine turns upside down again replaces the resin box turns over and cures the sand resin mixture under an oven. Once again I must note that it doesn't take very much time to complete the operation. This machine again runs on about a one minute cycle varying from that a little bit depending on the particular job that's being run. Sam is this shell making and core making operation shell molding is core of making operation is something brand new in the industry. Well it's not exactly new it's something that has been developing for a period of years and some companies make extensive use of it but it is a futures thing it will be more application in the future particularly shell cores they're quite new. You were talking a moment ago Sam about backing up the shells with shot what do you mean by that?
Well with the shell moldings since we have just a shell that covers the cavity for a particular casting when the castings are heavy they require some backup to keep the metal from breaking through the shell. We provide this support in the case of heavy castings with the use of shot which we dump down into a flask and support these shell molds in the flask. Why do you use shot why couldn't you use sand here again? Well sand can be used and is used in some cases but shot is a more is a heavier material and therefore gives a little better support than sand well. Is that actually shot to do you use in shotgun shell? Well no it's not exactly the same it's the shot that you would use in cleaning operations in the foundry. The shells were poured or put into a large container the shot was spread around them now they're about ready to start moving this machine. Sam that shaking I suppose is to shake the shot down solidly around the shell.
Yes there's to settle it down well along the sides of the shell so we get good even support. Sam here we've come now to the shake out machine which I understand is going to make a lot of noise and it is right now. Here's the mold coming up now what happens to it? This is the mold that you saw poured down on the other end of the foundry and we're now going to set the sand mold on this vibrating table which will shake away the sand and the sand goes down through a grate leaving the casting the hot casting on top of the table. All right what some of the amazing things that that I've seen here is the fact that this sand mold just falls away in this creating it drops down as he just told you into this large bat. Well now say we have all of these sand shaking away from the mold and the mold sitting there on the machine. Now what happens to it after that it's pretty hot right now. Yes it will be allowed to cool now and then go down to the cleaning room where the fine sand
that's stuck to the casting will be removed and then it will be ready to go to a machine shop for machining. Sam we've talked a lot about casting so I wonder if you could show us a typical casting that you use for your work here. Yes we have here a casting that is typical of one phase of the work that we do in the research foundry. We have here a mold for an engine head and we are developing the manufacturing process for this particular head and by that I mean the gating system how it will be made and how the metal will be introduced into this mold to get a sound good casting for production purposes and this is typical of some of the experimental work that we do for engineering will you actually be using this mold here to pour metal into this mold will actually be used to make an experimental casting the casting will be machined and go to one of our engineering departments where tests will be run on this
particular piece. Sam you mentioned a moment ago about the cleaning operation I think we ought to mention that we're standing right in front of a large cleaning machine the molds were shaken out a little while ago you heard that and they were brought over I guess put in this machine is that right Sam? Yes so this machine gives the the castings of blasting which removes some of the sand from it. We have an operator for this machine here that might give you a little detail of how this machine operates. Hey Sam. Another Sam. This is Sam dispenser here Sam what you like to explain how this machine works and what you do with it in cleaning castings. Yes I'd be glad to this machine here is what is known as a wheel operator and it's in the type of a table that revolves round and the reason it goes round so the shots that run and hit this hard surface bounces back to rubber fat and breaks up the shots in all different forms which shoots back to the object we have on the
table and we generally use flat objects in here most of the time and heavy objects which gives us a very good cleaner take all the sharp burrs off the articles that we put in here and plus the rust and dirt and sand that is accumulated and this is a finished project after we get through it. Where does it go from here? Well it generally goes mostly our product mostly goes to the machine shop and some of it is finished product which we send out right directly from here. That's a very large mechanism in there Sam and the shot flies around pretty rapidly does pretty rapidly and pretty strong too we control it by our gauges up there just everything about this machine is controlled according to timing that's very important what about the what about the danger of being hit by some of the shot? Well that's very very seldom because the man there's only one man that operates in the the man that knows how to operate it we don't let anybody operate any type of machine that's complete policy. Company takes a lot of safety precautions to
send it around my neck all the time especially in a foundry my friend. Okay Sam thank you very much. Now we've come over to the friction sign department L and it's going to be rather difficult to talk up this close to the saw but tell us exactly what friction sign is. Friction sign is the actually melding of a metal ahead of a saw blade or a strip of steel. Actually we don't need a regular saw blade we can use a piece of banding and the heat generated actually cut that metal. Now over there we're cutting a disc that would ordinarily not be saw well. Now in other words we couldn't cut that without this friction saw. Now wait a minute you mean to tell me that the air which travels in front of the saw blade actually cuts the metal. No it's the heat generated by the friction between the saw blade and the piece
part and the saw blade is about 24 feet long it's a very long blade and it is cool fast enough so that does not bell but rather the material which is in constant contact with it. Well that's what I was going to ask you why doesn't the saw blade mill but you just said how is it cool. It's just air cool. In other words just going through the air cools it off sufficiently prevent it from melding. Now that saw blade is traveling at about 136 miles per hour. It's a saw blade actually touching it's actually touching the metal that's right but not very hard. Well it's touching very fast in other words it's it's rubbing on the metal it and the metal both get hot but the saw blade being moving so fast does not pick up that heat but rather the part does. But the heat is actually what does the cutting. That's right. Well now you have a gentleman over here operating a machine and what if we could talk to him for just a minute. That's perfect. That's perfect man over there. Do you use any other blade besides the one you have on there now Fritz? Yes
you use any other blade on this machine you can cut the necklace still but when you flexion saw you see you take a old plate which isn't cut for necklace sawing anymore. The other tech is to speed it up because how does speed them back of it. It's a lot different from the old way isn't it? It sure is. What are you going to do with this file that you have in your hand Fritz? I just like to prove that we can cut a file which couldn't be cut in any saw or we couldn't even file it with that or saw but this plate will sure cut it and have. That sure does. The end of that file hot? Not very hot at all. Just a little heat but you can put your finger on there. We've come
now to what they call their centered metals. Now I don't know anything about this at all so you better start explaining from the beginning. Tell us what a centered metal is. Well a centered metal is a powdered metal. That's another term for it. It's a metal in a powdered form and we have a whole lot of different types here. Irons, coppers, they're mixed together and right here we have a press that presses them into the form desired and then they're taken over and heat treated or centered. In other words baked. In this little pan you have some rather copper colored powder. What is that? That is actually copper powder. You mean to tell me that this box full of powder is copper? That's right. Well how did you ever get copper into that form? Well we have an expert on this here. Mr. Harold Beale right over here. He's the engineer in charge and I think he can answer some of these more technical questions a lot better than I can. Harold, how do you get copper into that powdered form or how do you get any metal for that matter
into powder? The simplest way is to take the metal and burn it in air and in that form it becomes very brittle and is easily pulverized into a powdered material. Go ahead and the powder is again put through a treatment which reduces it back to the pure material. Is that the treatment that goes on right here in this machine? No the machine is a piece of machinery for molding this powdered material into some useful shape. For example this gear. In that particular shape the powder is held together only through a mechanical interlocking of the particles. The powdered piece in that form must be put through a furnace which bakes it and affects wells it together. Well now Harold I don't know whether this is all a brand new process or not is it? It's a very recent process as technical processes go. Certain phases have been in use for about 35 or 40 years whereas other products have only been under development for about 10 years
and this is the machine that does the business. That's right. I'll suppose we walk over here to this department and tell us a little bit about what goes on over here. I see a lot of equipment that looks rather interesting. Well this is our inspection department and we have a couple of pieces of equipment here that are quite unusual. I'd like you to meet George Dirks our inspector who can explain this equipment to you. George tell us about this particular piece of equipment right here with the VU meter as I know it but I suppose you call it something else. Yeah this is a surface finish indicator and this instrument we can determine where to finish the dust in this department comes up to specifications. Well now you have a piece of metal right here. What do you call that? This is a inner race of a ball bearing. The inner race of a ball bearing. Now where do you determine? How do you determine the surface or the thickness of the surface? Here
is a stylus where a small diamond is connected to an element and a tube in here and you move this over this surface. He's moving the stylus now within on the inside of that ball bearing base and it shows about a 10 micro -entrance in here. What does that mean George? Well it means 10 million of an inch are the peaks and valleys apart that is a very good finish for ball races. you
- Series
- Ear on Chicago
- Episode
- International Harvester Research
- Segment
- Part 1
- Producing Organization
- WBBM (Radio station : Chicago, Ill.)
- Illinois Institute of Technology
- Contributing Organization
- Illinois Institute of Technology (Chicago, Illinois)
- AAPB ID
- cpb-aacip-b27475a5236
If you have more information about this item than what is given here, or if you have concerns about this record, we want to know! Contact us, indicating the AAPB ID (cpb-aacip-b27475a5236).
- Description
- Series Description
- Ear on Chicago ran from 1955 to 1958 as a series of half-hour documentaries (130 episodes) produced by Illinois Institute of Technology in cooperation with WBBM radio, a CBS affiliate. Ear on Chicago was named best public affairs radio program in the metropolitan area by the Illinois Associated Press in 1957. The programs were produced, recorded, and edited by John B. Buckstaff, supervisor of radio and television at Illinois Tech; narrated by Fahey Flynn, a noted Chicago newscaster, and Hugh Hill, special events director of WBBM (later, a well-known Chicago television news anchor); coordinated by Herb Grayson, WBBM director of information services; and distributed to universities across the Midwest for rebroadcast.
- Date
- 1957-02-23
- Asset type
- Episode
- Genres
- Documentary
- Topics
- Education
- Media type
- Sound
- Duration
- 00:28:10.032
- Credits
-
-
Producing Organization: WBBM (Radio station : Chicago, Ill.)
Producing Organization: Illinois Institute of Technology
- AAPB Contributor Holdings
-
Illinois Institute of Technology
Identifier: cpb-aacip-146bb36bd12 (Filename)
Format: 1/4 inch audio tape
If you have a copy of this asset and would like us to add it to our catalog, please contact us.
- Citations
- Chicago: “Ear on Chicago; International Harvester Research; Part 1,” 1957-02-23, Illinois Institute of Technology, American Archive of Public Broadcasting (GBH and the Library of Congress), Boston, MA and Washington, DC, accessed August 10, 2025, http://americanarchive.org/catalog/cpb-aacip-b27475a5236.
- MLA: “Ear on Chicago; International Harvester Research; Part 1.” 1957-02-23. Illinois Institute of Technology, American Archive of Public Broadcasting (GBH and the Library of Congress), Boston, MA and Washington, DC. Web. August 10, 2025. <http://americanarchive.org/catalog/cpb-aacip-b27475a5236>.
- APA: Ear on Chicago; International Harvester Research; Part 1. Boston, MA: Illinois Institute of Technology, American Archive of Public Broadcasting (GBH and the Library of Congress), Boston, MA and Washington, DC. Retrieved from http://americanarchive.org/catalog/cpb-aacip-b27475a5236