Ear on Chicago; International Harvester Research; Part 2
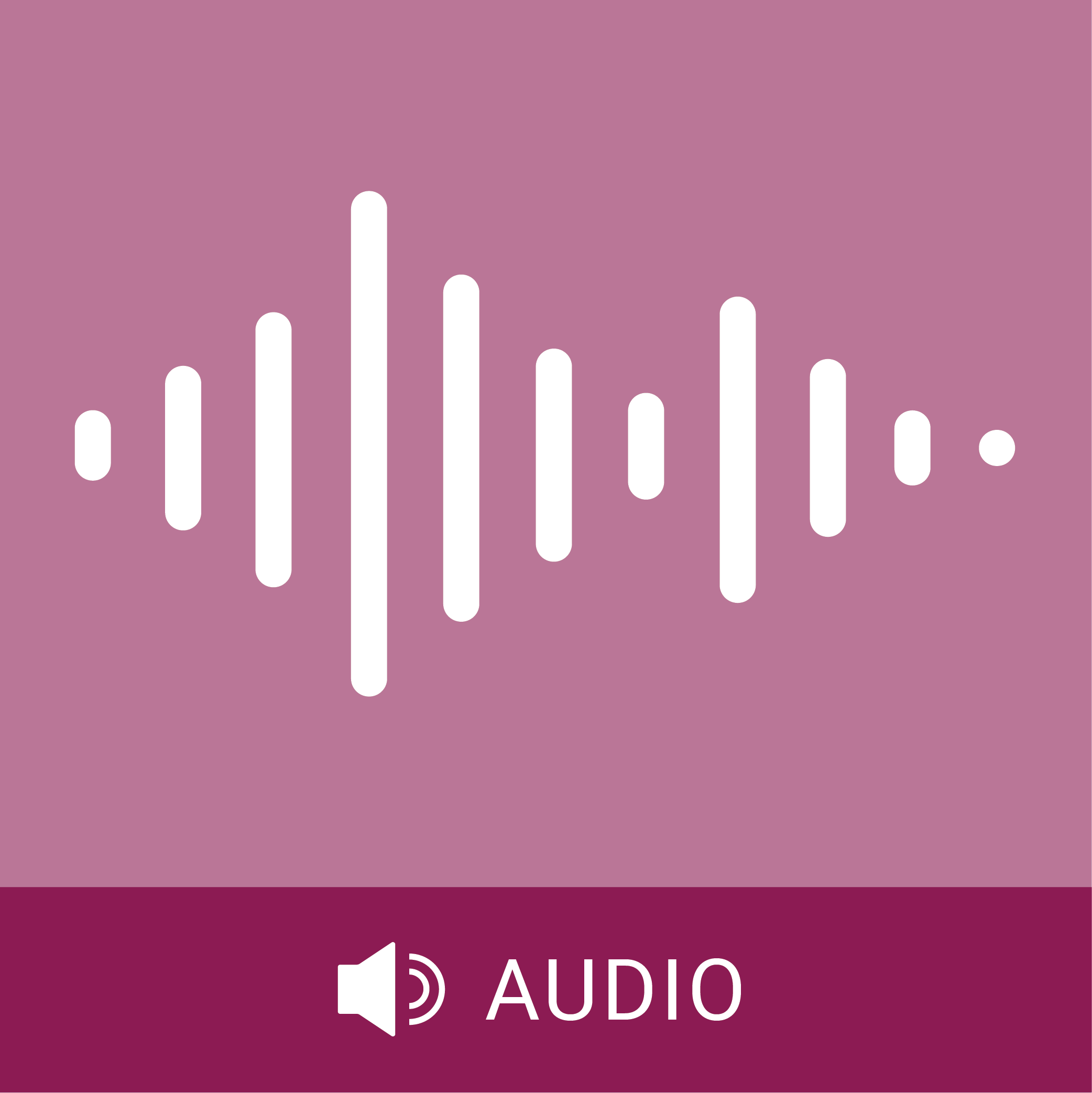
- Transcript
Sound you are hearing are those of a foundry foundry is located at the International Harvestor Company's Manufacturing Research plant which is located on Southwestern Avenue in Chicago. Today we are doing the story of this manufacturing research organization. Well we've come up to a rather well -rounded department of the organization in a large space area here and we were standing right in front of a machine which is sending sparks all over the place. Mr. Becker, what about this machine here that's sending out all these sparks? Is that a welding machine? Yes, this is a welding machine and at the present time we are developing procedures using this flash welding machine which is a method of resistance welding for fabricating two inch wrongs, a special situation which we are working on. Is that what you have in the machine now? Yes, we have a two inch wrong. Tell us something about the operation,
how it actually occurs inside that machine. The two pieces are to be welded, are loaded into the machine, the operator brings the two pieces together and a current flows between the two pieces creating the sparks as you see. Is that an electric current? That is an electric current, yes. The sparking or flashing as you see goes on for anywhere from one minute to a minute and a half and bringing the two faces up to a welding temperature. When that is reached the pieces are forced together under a forging action similar to the blacksmith type of forging. We hammer the two pieces together and that is what makes the weld. You will hear that come together very shortly. It just upset and the weld is finished now. I see, yes. Is this a strictly experimental? It is experimental as far as we are concerned here. However, after the procedure is developed, it will in turn be used in production. This process in its generalities
is used in production at the present time. Now what about inner gas arc welding, about which we have heard? That is one of the newest methods of arc welding which has come to be developed during the last six months or two years. We are standing in front of the arc welding machine right now, Mr. Becker. So suppose before he starts welding and we have to put on these masks, you tell us what happens. This is a method of arc welding whereby we feed the wire, which is the welding wire, down through a machine automatically. This wire is surrounded with a shield of gas. In this case, we are using carbon dioxide as a gas to shield the arc. In other cases, we can use other gases such as argon, helium and so forth. Now you told
us this was a rather new process. Is an arc welding an old thing? I have seen them do it for many years. Arc welding is a very old process. Old as far as relatively is concerned. However, as far as some of your manufacturing processes, arc welding is a relatively very new process. However, this particular inner gas shield and metal arc welding process, mig welding, some people call it, metal inner gas, is only approximately four years old. The portion that we are working on now is come into being only within the last six months or a year. During the early portions of the development, we were very active in the development of the process, working cooperatively with several industrial laboratories across the country. Well, Mr. Becker, before we turn this on, we are going to have to put on these big black shields that I have often seen welders use. But before we do this, would you tell me why we have to put the shields over our eyes? Yes, sir. The arc, as it is being made,
is very intense, is very bright. And if a man would look at the arc without the shielding, without the dark glasses, the ultraviolet rays from the arc would hurt his eyes. And he would just like sunburn. Or would he get sunburn from an arc? Is that right? Well, I suppose we are about ready now as he turns it on and goes to welding here. Or maybe I can describe inside this mass just what is going on. Would you like to go ahead? I have the mass gone now. And there is the welding going on and there is a green flame that I can see with a small wire going into the flame. The process only takes about six or seven seconds and I suppose you can hear the sputtering in the background. I'll let you listen. The machine was just shut off and now I guess I can take off the mass. Very fine, Mr. Becker. This is something rather new then and you are... Yes, very much so. This part that we are working on at the present time is a part for our products. Hank Coba here,
the operator can probably tell you a little bit about what this part is. Hank, what is it? Well, this happens to be a sprocket for a trasher, harvested trasher. Have you done this type of work for a long time, Hank? Oh, about 22 years. Is that right? Not the mig welding, but that's new, but then welding about 22 years. Okay, Hank, thank you very much for demonstrating it. Mr. Becker, there was a loud pop and here again is some welding. Tell us about this. Well, this is a one -phase welding. It's not exactly welding, it is cutting. We are making little pieces out of big pieces. What was a loud pop about? That loud pop was the operator lighting the torts. This is a oxyspedaline flame cutting operation whereby we use a... A lot of sparks flying across here. We are going to get burned up if we
don't walk away. Yes sir, this does create a lot of sparks and we should not be too close. The flame cutting operation that you see here is a method that we use quite frequently in our plants for preparing parts for welding. That is the reason why we have it under our welding section. Well, now there is a large slab of metal. What is that steel? Yes, that is steel and it... About three or four inches thick. I know sure that is a lot thicker than that. The piece that you see there is approximately six inches thick. Now, he is cutting right through that very easily. Yes sir, he cuts through it just like a piece of steel. The operation is very similar to a rusting operation. We are actually oxidizing or rusting the metal down to a narrow split. And when we russet the russ has no strength therefore the piece falls apart. Well, what is inside that mechanism to make that do that? What kind of chemical or whatever it is that you use? We are using at the present time we are using a combination of oxygen and a settling.
However, at the present time we are also experimenting with other fuel gas such as propane, natural gas and so forth. So, as a substitute for a settling. You find that a settling is still the best. There is some question in doubt. It may be for certain application the settling is the best. However, for other applications propane and natural gas are very, very satisfactory. Inside of this flame created by oxygen and a settling is a stream of oxygen. And the oxygen under a high pressure and velocity is what does the cutting. Okay, Mr. Becker, thank you very much for telling us about welding here in the department. Now, Mr. Drum, where do we go next? I see a big wall over here. What is behind there? Well, that is our X -ray laboratory behind that wall. If you would like to follow me, we will go into that laboratory and I will explain it to you. Fine. Mr. Drum, we have come out of the X -ray room and here
above us about six or ten feet off the floor is a large X -ray machine. As I understand it, you are not able to turn this on while we are in the room. Is that right? That is correct. That was why. Well, the reason is because the X -rays that are given off are harmful to the human body. How many votes does this machine have? This particular unit is a million volt unit. All right. Now, what do you use this X -ray unit for? We use this as a development tool as well as an inspection tool. Now, as a development tool, we will get a pilot casting as we call it out of the Foundry, or the first casting, and we will bring it in here in X -ray. It will determine whether there is any porosity present in the casting. Any what? Horosity. What would that be? Void. A cavity present. A hole in the eye. Yes, that is right. Do you mean to tell me you do that just as if the doctor looks at your ribs to see if they are broken? Or an arm to see if it is broken through an X -ray? That is the same thing. We place the casting on the table here, and we pass X -rays through the casting and they
contact the film. And we develop the film when we get what we call our negative or radiograph. Is this some of the film over here that you have developed? Now, what about this particular piece of film right here, where it has some sort of mold or casting that you have taken a picture of? And it has a word on their shrink. What does that mean? Well, that locates a shrink area. You notice a difference in darkness or intensity on the radiograph. This means that the molten metal, as it is solidified, shrunk away from that particular area and left this shrink area or void. Well, I can see that this X -ray machine is very important in your operation here then, isn't it? That is true. This particular unit will penetrate up to six inches of steel. Is that right? It has a sensitivity in the lower range that is sampled, say, three inches thick of 2 % sensitivity. In other words, we can find a cavity that is 2 % of the total thickness of the sample. Well, Mr. Drum, suppose you and I walk out of here
while the boys get back to work with their X -ray machine. Tell us where we go next. I'd like to take you to the Mechanical Engineering Section next. Now we have moved to another section of the organization and we'll go back to our guide, Mr. Drum, to tell us exactly what goes on here. Well, we are now in the metallurgical section, the physical testing area. Now, actually, the metallurgical section is quite a large section here at the manufacturing research. We have chemical laboratories, a physics section, induction heating and heat treat section. But we are now, as I mentioned, in the physical testing area. Now, Mr. Hoggren, one of our supervisors here, will explain more. Mr. Hoggren, I suppose we ought to start with a piece of equipment that we're in front of. Tell us about this. This is a tensile testing machine. It has 400 ,000 pounds of capacity. We can push, we can pull, we can ban, or we can twist, with very great accuracy within one half of 1 %
of the measured load. The machine is now being used to tensile test a bolt. This bolt is one and a half inches in diameter and attached to the bolt, you will see what we call an extensometer. This is used to measure the stretch in the bolt. By measuring the stretch, we measure the yield point of the bolt. The operator has now reached the yield point. He will now remove the extensometer in order to prevent damage to it, and he will continue with breaking the bolt. This entire test will take less than 30 seconds. Now, you're pulling this bolt apart, is that correct? That is correct. It makes quite a noise when it breaks. There's a lot of energy expended. Is it about to break? It's getting very close. It has their pastage. There it goes.
You mean to tell me that was a bolt coming apart that sounded like a crack of a cannon almost? That is correct. Bill? How many pounds did that take? 245 ,000 pounds. It took 245 ,000 pounds of stress to pull that bolt apart. Is that it? That's right. Is that high or low? A little higher than average for this bolt. Why do we pull bolts, Bill? Well, international harvester makes approximately a million bolts a day, and they buy approximately the same numbers. So it's pretty important the specifications to be rigid for this material. Now, when we hear that bolt pull apart, it creates a large sound. And here, Kirk Logi has just brought the bolt over to us. We see where it has pulled apart. Actually, is this metal stretched somewhat? Yes, that metal has stretched. This bolt is probably stretched. Oh, and a good eighth of an answer more in breaking. Now, we've come to what they call the fatigue machines. Would you
explain what these are, Mr. Hogger? You just saw a static test where we break a part with one application of load. Now, we find that if we apply a lower load for many more cycles, we can also break the part. And instead of deforming, the part will break as if it is brittle. The ordinary layman calls this crystallizing. The metal is crystallized. Actually, the metal is crystal in the begin with. It never can crystallize anymore. Here, we have a large machine. This is a 300 ,000 -pound inch capacity machine. We are testing the bending strength of a single tooth. In order to evaluate different heat treatments for this large gear, there is no other equipment around a country that could test this gear in assembly, except the actual part that it used in. But here, by adapting it to a fatigue
machine, we can evaluate heat treatment and materials in this gear. We've come over a short distance away now from the other part of this particular metallurgical section, and to what they call induction heating. Do you tell us what induction heating is and what you do here with this machine, Mr. Hogger? Well, I'd like to turn this over to Jack London, a moment, who has been charged with this project. Now, Jack, what does this do? Well, our general problem back here is to surface iron steels, similar to your conventional carburizing methods. We obtain surface hardness, as only we use a high -frequency electrical power. And what we do, we induce it into a plain copper coil that's wrapped around the area one to heart. In other words, we can selectively heat a certain area on a part without affecting the other part of
the steel. So, we induce a magnetic field in this coil, and the resistance of the material, steel material to this magnetic field, causes it to heat up in a matter of seconds. Well, in your regular conventional method, you have to put it in a furnace and it takes an hour, and if your carburizing might take 15 hours to obtain, we can obtain in a matter of less than a minute. If you do this heating by radio waves, that's it. This piece of equipment we have here is a 200kW radio frequency generator, and with a few additions, it could be made into a regular broadcasting station, as well. 200 ,000 watts. That's right. That's stronger than anything we have in the Chicago area. That's right, it's about four times. Well, what do you do with them in the area? Does that signal get out and interfere with radio sets or television sets? No, it's very well shielded, and we have to have a certificate from the FCC to make sure that there isn't any interference in the area, and we've been running for about eight years now, and we have many complaints. Well, suppose you describe how this
operation takes place, Jack. All right, we're going to heat this gear now. It's in what we call the AF station, which is audio frequency. I'll now push the button, and the gear and the air cylinder will... It came up in the place inside the coil. It's rotating inside a copper coil. The heat will now come on. The heat's on. The part is starting to heat up right now. It's starting to get red. This total operation will take about 20 seconds. As soon as it's up to a certain temperature, the heat will kick off. You can see the red now. When the heat kicks off, the gear will drop out of this station, and we will move it over the RF station. The coil has just dropped down now from what Jack was telling you. It's fire red. It looks like it's beginning to cool a little bit. It'll cool down to about 1 ,100 degrees. And at that time, the RF will come on. There it is. It's only one in four, ten seconds, and a spray quench hits it immediately, and the gear is hard.
Many advantages to this operation. It's very fast and very clean of working operations. There isn't much dirt or heat, and we obtain very good hardness. The spray of water is going all over the piece of equipment that he's got in there. I'm standing back because he's opening up the window, and the water will able to splash all over us here. Jack, one question before we leave. This, of course, is not manufacturing. This is research, is that right? That's right. We have a quite well -rounded induction heating section. Besides this equipment we're working on right here, we have progressive hardening equipment, where we can take a long shaft and pass it right through a coil, and it heats and quenches as it passes through. Our main problem here is to develop new cycles for new parts, experimental parts, to design inductors, and we work with our physical test section, who determines
the wear resistance and the fatigue strength of these parts. We do a lot of work on gears. Well, Mr. John, we've come to a new section now. This is Materials Handling and Packaging section, as you call it, but perhaps you better explain that a little more thoroughly. We just heard a loud crash, and saw something that we'll describe in just a moment, but first of all, tell us what happens. Well, that was an incline impact test that you heard. We were performing a test on that, impacting a crate against a backstop, simulating the rough handling or humping of a box car. The Materials Handling section devotes their work to our investigations of handling, as well as packaging of materials. Now, Al Bach here, one of the supervisors, will explain the operations of the department to you. Now, let's start with this incline impact tester, and that's just a name to me, except that we can see, obviously, what it is. Up the little incline here
goes a large box of gears, and then all of a sudden you let it loose, and it goes against some sort of a wooden wall. How do you use this equipment? Well, I was used to simulate the impacts that containers received during shipment. And test boxes that way? That is correct. You can test the container with its contents to see what the effects of impacts would be. Now, they're going to operate this machine again. I'd like to see it go once again, and we can hear it go. And as it goes, you might tell us just exactly how it works. First of all, these gears engage down here, and it starts to go up the incline. If you can picture two car rails, ten -degree angle, which is mounted a platform with wheels, and out this platform is the wooden container, and it is raised by means of a conveyor to a predetermined height and then released. And the greater the distance, the greater the impact you receive of your container. What have you got at about four and a half feet there now? Well, what it
amounts to is approximately ten mile per hour impact. Well, there was an awful racket if I've ever heard one. Now, what was that? Well, that's our vibration testing machine is used to simulate the vibrational stresses that containers received during shipment. Well, I imagine that it gets a lot of stress and strain on it, doesn't it? Yes, it does. It's one of the series of rough -hamming tests that we subject containers to. Is this the same thing as we see over here, except that isn't a wooden box? That's a steel container, that is correct. You have gears or something inside of there? Well, what's inside of that is gray iron castings, scrap forging. And large, how does it shake? What if you've got some sort of equipment underneath or a machine underneath to just keep it shaking up and down? Well, if you can picture a flat board with a small block mounted on top and you keep bouncing this board up and down, it's the same action that you get on this machine. And the more rapid the speed, the greater the stress is that you
impart to that container. That's the same stresses and strains it would be subject to if it were shipped by rail. That is correct. That is correct. I see. Now we've moved over here to where a gentleman has been dropping a box from about four feet down to the floor. What is this equipment? Let's see. A tester that works under free fall, principal. It tests the rough handling of cartons. Suppose we'll let Tom Preach explain it to you. All right, Tom. Now, you're about ready to drop a small package here. I suppose the reason for that is to just see how much stress and strain it will take in handling. This simulates what it would go through in handling, is that right? Yes, sir. This drop tester determines whether or not a container will sufficiently protect the product that is inside of it. Why don't you drop this one? Let's see if it'll break. Of course that one did not break, and I don't suppose it was supposed to,
but how often will that go through that type of test? This container will be dropped on each corner and each flat surface of the container, which is a total of 12 drops. And if it doesn't break then, why it's in pretty good shape? Yes, sir. In the contents, if they're in good shape, we say that the product is packaged sufficiently. Now, here is another testing machine, which is, I suppose, testing the strength of paper, because you're snapping little holes in the piece of paper here. That is correct. It determines the resistance to bursting in paper materials. I see. Now, how much pressure is applied to this equipment or to this paper right here? Suppose we let Dave D's explain that. Now, suppose you snap another piece of paper here for us, let's see how much it goes up.
The indicator, of course, starts at zero, moves all the way up, it could go up to 200. That's right, and this will record a maximum. Now, that's snapped at almost 99, I suppose, isn't it? Yes, right around 99, that's about hitting the average. Now, there's some more equipment over here, which you might explain. Here's a large, what is this, a roll of paper that's being moved around here? This isn't paper at all, is it? This is our scuff tester. This machine is delivering 60 cycles exactly to the minute, and this cam will give it two scuffs per second, so we're getting 120 scuffs per second. This determines the abrasion effect of paper wrapping on materials. Let's listen to that for a minute. Now, over here is another calibrated scale, and why don't you tell us what this is? Well, this is our puncture tester. It simulates damage to a carton, just as though it were hit with a corner
of another carton. You can see the head here. The weight will enter it is a corner, it's a pyramid, but I'll show you how it works. This will put in a panel, which would be... It's wood, it's probably similar to one of our wire bond boxes. And because it is very strong, we put added weights to the pendulum to give it more energy when it hits. Okay, start it up. Now, you see, it penetrates a panel here, and we can take a reading on this lower steel. Well, that just about clears us up in this particular materials, handling and packaging section. Doesn't that, Mr. Drum? Yes, it does. I would not like to take you back to our assistant manager's office. Mr. Evans, and I think he can answer any further questions you might have about our organization. Fine, thank you very much. Mr.
Hill, we have enjoyed and appreciated the opportunity to describe some of our activities concerned with the development and improvement of several manufacturing processes widely used by our company. You have seen our facilities and the work we are doing, but little has been said about the most important single item, people. Without the technical skills and know -how, the ability to think creatively and work together, little would be accomplished. It is generally recognized that an organized approach by capable people is essential to continuing progress in this type of operation. In this respect, we have been extremely fortunate. Also, I would like to point out that what you have seen here represents only a small portion of the company's overall research and development activities. Each of our manufacturing plants and engineering departments has personnel and facilities assigned to the development and application of new ideas related to their particular fields of interest. Many of the items you saw during your tour of the laboratory are being worked out in cooperation with others throughout the country. Through the participation of our people in
the activities of technical societies and representation on advisory committees of universities and the military, the results of many of our projects are coordinated with the work of other laboratories. Through this cooperative effort on problems of mutual interest, it is possible for all of us to progress much more rapidly. We also have programs related directly to our products, which are of a competitive nature and not discussed outside the company. A very significant factor in the success or failure of a company today is its ability to keep abreast or ahead of others in the design of its products and its methods of manufacture. The fact that we live in a country where it is possible for industry, universities, and the government to work together toward technical progress and at the same time, all strive to get there first is something for which we can all be proud and thankful. We have the highest standard of living in the world today, yet based on the backlog of new ideas yet to be exploited, as well as our potential for further development, I doubt if it is possible to visualize how much better off we will be in the future.
- Series
- Ear on Chicago
- Episode
- International Harvester Research
- Segment
- Part 2
- Producing Organization
- WBBM (Radio station : Chicago, Ill.)
- Illinois Institute of Technology
- Contributing Organization
- Illinois Institute of Technology (Chicago, Illinois)
- AAPB ID
- cpb-aacip-5de72877242
If you have more information about this item than what is given here, or if you have concerns about this record, we want to know! Contact us, indicating the AAPB ID (cpb-aacip-5de72877242).
- Description
- Series Description
- Ear on Chicago ran from 1955 to 1958 as a series of half-hour documentaries (130 episodes) produced by Illinois Institute of Technology in cooperation with WBBM radio, a CBS affiliate. Ear on Chicago was named best public affairs radio program in the metropolitan area by the Illinois Associated Press in 1957. The programs were produced, recorded, and edited by John B. Buckstaff, supervisor of radio and television at Illinois Tech; narrated by Fahey Flynn, a noted Chicago newscaster, and Hugh Hill, special events director of WBBM (later, a well-known Chicago television news anchor); coordinated by Herb Grayson, WBBM director of information services; and distributed to universities across the Midwest for rebroadcast.
- Asset type
- Episode
- Genres
- Documentary
- Topics
- Education
- Media type
- Sound
- Duration
- 00:28:49.032
- Credits
-
-
Producing Organization: WBBM (Radio station : Chicago, Ill.)
Producing Organization: Illinois Institute of Technology
- AAPB Contributor Holdings
-
Illinois Institute of Technology
Identifier: cpb-aacip-07ada87ed17 (Filename)
Format: 1/4 inch audio tape
If you have a copy of this asset and would like us to add it to our catalog, please contact us.
- Citations
- Chicago: “Ear on Chicago; International Harvester Research; Part 2,” Illinois Institute of Technology, American Archive of Public Broadcasting (GBH and the Library of Congress), Boston, MA and Washington, DC, accessed August 10, 2025, http://americanarchive.org/catalog/cpb-aacip-5de72877242.
- MLA: “Ear on Chicago; International Harvester Research; Part 2.” Illinois Institute of Technology, American Archive of Public Broadcasting (GBH and the Library of Congress), Boston, MA and Washington, DC. Web. August 10, 2025. <http://americanarchive.org/catalog/cpb-aacip-5de72877242>.
- APA: Ear on Chicago; International Harvester Research; Part 2. Boston, MA: Illinois Institute of Technology, American Archive of Public Broadcasting (GBH and the Library of Congress), Boston, MA and Washington, DC. Retrieved from http://americanarchive.org/catalog/cpb-aacip-5de72877242